Downloads
Specifications
Cad Models
Support
Multi-fingered programmable grasper
The BH8-series BarrettHand™ is a multi-fingered programmable grasper with the dexterity to secure target objects of different sizes, shapes, and orientations. Even with its low weight (980 grams) and super compact (25mm) base, it is totally self-contained. Communicating by industry-standard serial communications or high-speed CANbus (USB adapters included), integration with any arm is fast and simple. The BH8-series immediately multiplies the value of any arm requiring flexible automation.
As an intelligent, highly flexible eight-axis gripper, the BarrettHand BH8–282 reconfigures itself in real time to conform securely to a wide variety of part shapes without tool-change interruptions. The grasper brings value to automation because it: reduces the required number and size of robotic workcells while boosting throughput; consolidates the hodgepodge proliferation of customized gripper-jaw shapes onto a common programmable platform; and enables incremental process improvement and accommodates frequent new-product introductions, capabilities deployed instantly via software across international networks of factories.
The BarrettHand neatly houses its own communications electronics, servo-controllers, and all four brushless motors. Of its three multi-jointed fingers, two have an extra degree of freedom with 180 degrees of lateral mobility supporting a large variety of grasp types. All joints have high-precision position encoders.
Check out our Industrial Robotics YouTube channel→
WHY BUY A BARRETTHAND™ WHEN PARALLEL-JAW GRIPPERS ARE SO CHEAP?
Each gripper must be custom designed. Grippers require specialists to design, fabricate, and debug specially-shaped finger surfaces for each part shape and for each unique part orientation.
Unless the host arm will perpetually perform the same task, it needs an infinitely variable supply of grippers and the ability to switch between them instantly as the part shapes and orientations change. A robot arm exchanges grippers with either a turret or a tool changer. A turret is limited to switching between 2 or 3 grippers. A tool changer can handle a large number of grippers, but at the enormous costs of wasted space from storage fixtures and badly increased cycle times.
Combined with its versatile software routines, a single BarrettHand matches the functionality of an endless set of custom grippers—yet switches part/tool shapes electronically within half a second.
The BarrettHand integrates with your application by consolidating many custom gripper tools into a single smart grasper. It is shipped as a complete turn-key system.
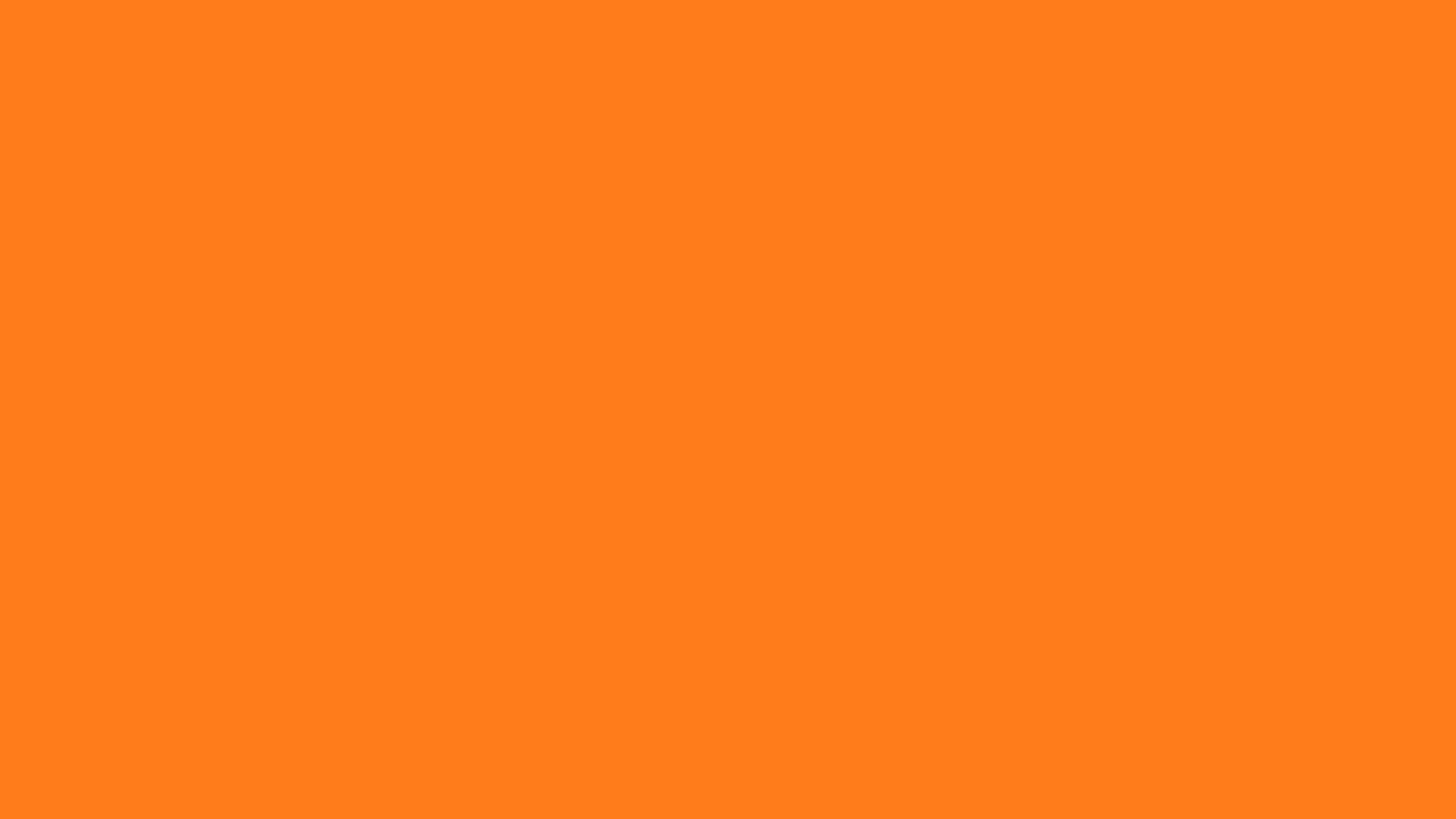
Software and Options
-
PyHand allows a user to manipulate joints, read sensors, and perform hand maintenance routines.
-
Libbarrett is Barrett’s real-time controls library. Written in C++, it runs Barrett Technology's products, including the WAM Arm and the BH8-280 BarrettHand. The library provides both a high-level interface (initialize the Hand, move the WAM to a position in joint-space, etc.) and a low-level interface (for performing torque calculations in hard real-time).
For further information, see the Libbarrett support page.
-
Barrett's Perception Palm contains two CMOS video cameras, a laser-projector, an infrared rangefinder, and an illumination LED all within a high-impact polyurethane resin housing that is mounted directly on the palm of a BarrettHand! The Perception Palm augments the contact-based localization sensors already available on the BarrettHand (6-axis force/torque sensor, fingertip torque sensors, and tactile sensing) with several noncontact sensors to provide valuable localization information in the critical time just before manipulation, but after base-mounted sensors may have become occluded by the manipulator itself. Gorilla Glass is used for sensor and emitter lenses, providing impact and scratch resistance, and making it perfectly safe to manipulate objects up against the surface of the palm.
The Cameras: The Perception Palm offers uncompressed streaming video from dual cameras at a resolution of 320x240 (16 bits per pixel) at 30 frames per second. If you prefer to take snapshots, each camera's native resolution is 1600x1200. With a minimum focal distance of just 6 cm, you can obtain high-resolution image data up close to your manipulation target. At this distance, you can identify surface textures, colors, and materials more accurately.
The Laser Projector: When used in conjunction with the camera data, you can generate highly-accurate depth information based on the deformation of the structured light emitted by the laser projector. This helps with object segmentation and leads to more accurate mapping of the local scene.
The Infrared Rangefinder: The IR rangefinder has a 4-50 cm range, so it is ideal for non-contact localization when approaching a manipulation surface such as a table or floor.
The White Illumination LED: This controllable, locally-integrated light source helps to cast out shadows caused by manipulator interference between an overhead or base-mounted light source and the manipulation target. Dexterous illumination can help the robot see into areas of the workspace that are insufficiently lit by other means.
Simple USB: All of the Perception Palm sensors operate over a single USB 2.0 connection. USB offers familiarity, ease-of-use, cross-platform compatibility, quick-disconnect, and hot-plug capability.
-
The Barrett 6-Axis Force/Torque Sensor is a completely self-contained sensing package that expands the force sensing capability of WAM™ and BarrettHand™ systems. The Force/Torque Sensor is available as an option when purchasing a WAM Arm or BarrettHand. The base of the sensor attaches to the tool plate of the WAM Arm (4-DOF and 7-DOF)* and the top plate of the sensor attaches to the base of the BarrettHand 28X series.
As with the BarrettPuck™, the Force/Torque Sensor is an entirely self-contained unit. There is no need for an external cable or large controller unit; all of the necessary amplification and processing electronics are built into one of the industry’s thinnest packages. With the calibration data preloaded into the sensor’s non-volatile memory, the onboard 32-bit DSP processes signals from all the strain gages and outputs 3 forces and 3 torques. All that is needed to start taking measurements are Barrett’s standard internal 48-V power and CANbus communications.
Manufactured from precision machined high-strength aircraft aluminum (7075-T6) and grade 5 titanium, the package is light and strong. Bonded silicon strain gages (up to 75 times more sensitive than foil gages) enable force-sensing resolutions of less than 10 grams while maintaining a maximum overload limit that is 20 times the operating range.
-
Several optional fingertip configurations are available to further enhance the capability of the standard BarrettHand. Tips are easily changed, encouraging user customization. A standard BarrettHand can be commanded to grasp gently or firmly. Optional fingertip strain-gage sensors independently measure torque at each fingertip joint, providing additional user feedback.
-
Item description